Aluminum is one of the most widely used alloys in modern production, and aluminum seems to be the best material. It is light, strong, durable, and corrosion-resistant. This is why the new milling aluminum strategy has been developed rapidly.
One of the modern successful CNC aluminum milling methods is high-speed machining. The main difference compared with conventional milling is that the speed of high-speed milling is much higher, and the machinist can use them to increase the cutting feed. High-speed milling is different from conventional milling. This is a more productive and innovative way to produce small batches of parts and prototypes. The evolving metal industry requires rapid production of parts. Every month, the requirements for customized parts or rapid prototypes are getting higher and higher. More and more customers want to complete orders faster. They also want these components to have higher accuracy than before.
What is High Speed Machining?
Originally developed by German inventor Dr. Carl Salmon in the 1920s, high-speed machining was born when its originator realized that for a specific workpiece metal, the heat generated at the interface between the cutting tool and the workpiece would peak at a certain critical spindle speed.
Ordinary milling processing uses low feed speed and large cutting parameters, while high-speed milling processing uses high feed speed and small cutting parameters. Compared with ordinary milling processing, high-speed milling processing has the following characteristics:
(1) High-Efficiency
The spindle speed of high-speed milling is generally 15000r/min~40,000r/min, up to 100000r/min. When cutting steel, its cutting speed is about 400m/min, which is 5-10 times higher than traditional milling processing. When processing mold cavities, it is compared with traditional processing methods (traditional milling, EDM, etc.) Its efficiency is increased by 4 to 5 times.
(2) High-Precision
High-speed milling processing accuracy is generally 10μm, and some accuracy is even higher.
(3) High Surface Quality
Since the temperature rise of the workpiece during high-speed milling is small (about 3°C), there is no metamorphic layer and micro-cracks on the surface, and thermal deformation is also small. The best surface roughness Ra is less than 1μm, which reduces the workload of subsequent grinding and polishing.
(4) It Can Process High-Hard Materials.
It can mill 50-54HRC steel, and the highest milling hardness can reach 60HRC.
Advantages Of High Speed Machining For Aluminum Milling
Due to the characteristics of HSM, HSM milling aluminum is very advantageous in many unexpected aspects. By choosing an HSM strategy for aluminum instead of using conventional milling, you will get the following benefits.
Improve efficiency
The cutting speed of high-speed milling can reach three times the traditional milling speed. When machining softer aluminum alloys, it can even be doubled.
As far as we know, the machining feed is a parameter that defines the productivity of the entire milling process. That is, compared with conventional milling, high-speed machining efficiency can be much higher. The machinability of aluminum makes it possible to increase the spindle speed to 18,000 rpm or higher.
Such a high material removal rate makes aluminum machining services using aluminum’s HSM strategy a very favorable product for the automotive and aerospace industries. In the first case, the car prototype requires a lot of material removal, preferably with as few milling settings as possible. In the second case, there are many long and large parts with deep pockets (they must be light, so most of them are processed into a set of intersecting ribs) and thin walls. In addition, aluminum alloys account for aircraft and rockets. 80%. .
Notch Temperature
Studies have shown that the cutting temperature changes with increasing speed. At the beginning, as the speed increases, the temperature also increases. However, further, the temperature dropped sharply. This gets to a point where it does not matter. Increasing the cutting speed will eventually only lower the temperature a little bit. This change is ideal for high-speed milling.
For example, when milling aluminum at a speed of 300-500 m/min, the temperature may reach 600 to 800 degrees. However, when we increase the speed to 1200, the temperature will drop to less than 200 degrees, and the temperature is only 150 degrees at 1800 m/min. From now on, it does not make sense to cut faster.
From the right perspective, it is only 150-200 degrees. Local heat treatment will not cause changes in material properties in this area. The metal particles will not increase, and the cooling requirements are much smaller. This is an obvious advantage.
Extend Tool Life
This seems strange due to the high speed involved. Therefore, it is generally assumed that tool wear must be higher. However, when we compare it with the amount of material cut by traditional milling, the difference is obvious. In terms of tool life for high-speed milling aluminum, the clear winner.
You might be wondering what contributes to extending tool life? First, the cutting temperature is significantly reduced. This means higher tool material strength. In addition, the chip width is small during high-speed milling. This is because despite the increase in feed, the tool rotates faster and can cut thinner chips.
In addition, when machining aluminum, one of the main problems is that aluminum is too soft and sticks to the cutting edge of the tool during machining. This reduces the sharpness of the tool and increases the cutting force, thereby shortening the tool life.
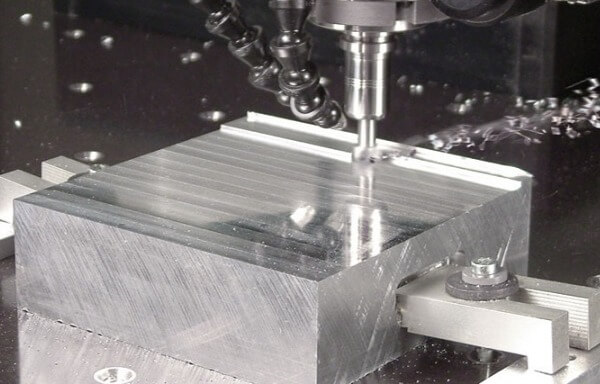
Precision of high-speed milling aluminum
We all believe that a higher feed rate will reduce the finish of the aluminum surface, because the cutting edge of the tool can go farther, and the tool can turn and cut. Generally, this leads to wider chipping, higher cutting forces and poorer surface finish. However, in HSM, despite the large feed rate, the tool speed is higher, so the chips are actually thinner than in conventional milling. In addition, due to the small cutting force, the vibration is small. These features all help improve accuracy.
Low Coolant Usage
Some HSM strategies for aluminum processing do not use coolant at all. Processing at 200 degrees almost does not require cooling materials and tools. However, some extremely precise operations still use coolant to improve the quality of parts, but the amount of coolant is much less than that of conventional machining. Some aluminum high-speed milling processes use so-called minimal lubrication. The amount of cooling liquid applied is only sufficient to form a film, thereby reducing friction and providing some cooling, so the amount of cooling liquid required is usually small.
Constant Tool Engagement Angle
One of the main problems when milling a cavity with an end mill is to make the cavity angle. The end mill must be rotated 90 degrees to create a cavity, and at this time, the material it cuts must be doubled (from both sides of the cavity). This leads to a local increase in cutting force and is very detrimental to tool life and part accuracy. However, HSM aluminum milling has many predetermined tool path generation strategies, including a constant tool engagement angle. This means that when machining all the material surrounding it on a circular path, the tool gradually approaches this angle. In this way, the cutting force remains constant and the accuracy remains the same. In addition, tool life can be extended.
SANS Machining is concentrated on CNC machining manufacturing, prototype machining, low-volume manufacturing, metal fabrication, and parts finishing services, provide you the best support and services.
Any questions or RFQ for metal& plastic technology and custom machining, welcome to send an inquiry to us.