Titanium and alloys use its unique properties to be more and more widely used in aerospace and biomedical fields. This popular metal has anti-rust and anti-chemical effects, can be recycled, and has light weight, high strength and excellent corrosion resistance, which solves many engineering problems. Titanium parts last longer and provide better performance and results than other metals and materials.
Titanium is 30% higher than steel, but nearly 50% lighter than steel. Titanium is 60% heavier than aluminum, but its strength is twice that of aluminum. However, when machining titanium alloys and selecting the right tools and parameters, some challenges must be considered.
Here we have an in-depth understanding of titanium machining, why it is so difficult to process titanium, and provide some technical insights and tips that can improve the success rate of titanium processing, also include its benefits and application.
Titanium Machining Varieties
There are many grades and varieties of titanium alloys, more than 100 kinds. Each alloy has its own unique properties and properties. 40-50 kinds are available in industry, and more than ten are the most commonly used. Including various tastes of industrial pure titanium and selected titanium alloys, such as Ti-6AL-4V, Ti-5AL-2.5Sn, TI-2AL-1.5Mn, Ti-3AL-2.5V, Ti-6AL- 2Sn-4Zr-2Mo, Ti-6AL-2Sn-4Zr-6Mo, and Ti-10V-2Fe-3AL and Ti-0.20Pd, T-0.3Mo-0.8N, etc. However, for most countries, the first two important alloys (Ti-6Al-4V, Ti-5A-2.5Sn) are the most typical, and they are also recognized by the world.
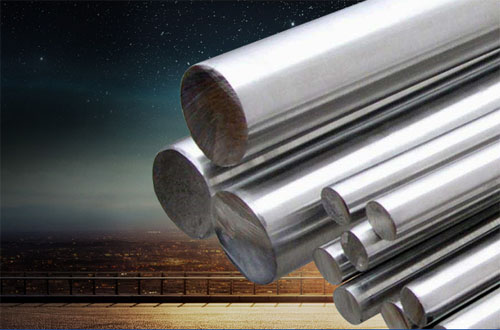
According to the organization classification, titanium alloys are divided into the following three categories: α alloys, (α+β) alloys and β alloys.
α Titanium Alloy
It is a single-phase alloy composed of α-phase solid solution. It is α-phase regardless of normal temperature or higher practical application temperature, with stable structure, higher wear resistance than pure titanium, and strong oxidation resistance. At a temperature of 500°C to 600°C, it still maintains its strength and creep resistance, but cannot be strengthened by heat treatment, and its room temperature strength is not high.
β Titanium Alloy
It is a single-phase alloy composed of β-phase solid solution. It has high strength without heat treatment. After quenching and aging, the alloy is further strengthened. The room temperature strength can reach 1372 ~ 1666 MPa; but the thermal stability is poor and it is not suitable for use at high temperatures.
α+β Titanium Alloy
It is a dual-phase alloy with good comprehensive properties, good structural stability, good toughness, plasticity and high-temperature deformation properties, and can perform hot pressure processing well, and can be quenched and aging to strengthen the alloy. The strength after heat treatment is about 50%-100% higher than the annealed state; the high-temperature strength is high, and it can work for a long time at a temperature of 400℃~500℃, and its thermal stability is second to that of α titanium alloy.
The most commonly used of the three titanium alloys are α titanium alloy and α + β titanium alloy. α titanium alloy has the best machinability, followed by α + β titanium alloy, and β titanium alloy is the worst.
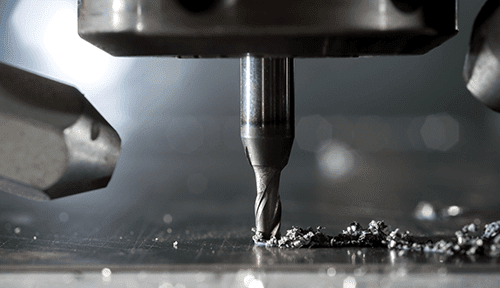
Why is titanium difficult to machining?
Physical phenomena of titanium machining
The cutting force during processing of titanium alloy is only slightly higher than that of steel of the same hardness, but the physical phenomenon of processing titanium alloy is much more complicated than that of processing steel, which makes titanium alloy processing face huge difficulties.
The thermal conductivity of most titanium alloys is very low, only 1/7 that of steel and 1/16 that of aluminum. Therefore, the heat generated in the process of cutting titanium alloy will not be quickly transferred to the workpiece or taken away by the chips, but will be concentrated in the cutting area. The temperature generated can be as high as 1,000 ℃, causing the cutting edge of the tool to quickly wear, crack and Generate built-up edge, wear blades quickly appear, and generate more heat in the cutting area, further shortening the life of the tool.
The high temperature generated in the cutting process also destroys the surface integrity of the titanium alloy parts, resulting in a decrease in the geometric accuracy of the parts and a work hardening phenomenon that severely reduces its fatigue strength.
The elasticity of titanium alloy may be beneficial to the performance of parts, but in the cutting process, the elastic deformation of the workpiece is an important cause of vibration. The cutting pressure causes the “elastic” workpiece to leave the tool and rebound, so that the friction between the tool and the workpiece is greater than the cutting action. The friction process also generates heat, which aggravates the poor thermal conductivity of titanium alloys.
“Hot” is the “culprit” in the difficult processing of titanium alloys!
How to improve the Titanium Machining?
On the basis of understanding the processing mechanism of titanium alloys, plus previous experience, the main technological know-how for processing titanium alloys are as follows:
More coolant
Titanium is an insulator, so the heat generated during the cutting operation tends to stay near the cutting tool. One obvious way to deal with excess heat is to add coolant. The working area and tools are sandblasted with 10% concentrated coolant supplied by high pressure to ensure that the contact area remains cool and all heat-carrying chips can be washed away.
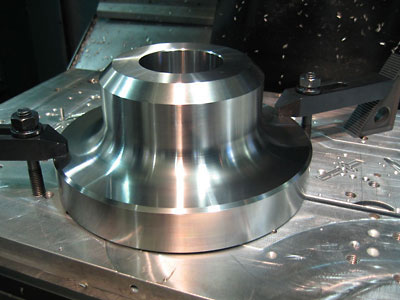
High-pressure coolant
For turning applications, the location and pressure of the coolant are critical. With the correct application, higher surface speeds and metal removal rates can be achieved. The only disadvantage is that the underlying material will redeposit on the surface of the part. This can be overcome by planning the cutting strategy and reducing the coolant pressure for the final finishing.
Constant feed
Titanium is easy to work hardening, that is, when cutting materials, titanium becomes harder and therefore wears more tools. The constant feed ensures that the machining hardened material is kept to an absolute minimum.
Increase the feed rate
If the machine allows it, increasing the feed rate means that the tool spends less time in a specific area, so there is no more time for heat accumulation and work hardening to affect the cutting edge of the tool.
Tooling
The PVD coated carbide tip is the most suitable tool for cutting titanium. Newer and more advanced tool coatings can also be provided, such as TiAIN (titanium aluminum nitride). Titanium is an elastic material, so this sharp tool is absolutely essential. Blunt tools will wipe the surface and cause jitter.
Chip control
Titanium produces long chips, which can easily damage the tool and mark the surface of the workpiece. In addition, long, thin chips are not ideal because they do not help transfer heat away from the work area. Therefore, when machining titanium, ideal tools and tool paths are ideal for making smaller and thicker chips.
Tool path
Choosing the right tool path when machining titanium is as important as choosing the right tool. When machining titanium, it is absolutely necessary to ensure that the tool path always engages the workpiece. When cutting a groove, the tool path combined with a cycloid pattern will reduce the time for any groove to engage with the material, which helps limit heat accumulation. Driving the cutting tool into and out of the workpiece helps reduce shocks and sudden movements that can severely damage the tool.
Machine tool
A robust machine tool is essential for the successful machining of titanium. The ideal titanium milling machine must be rigid, and the spindle must be able to run at low spindle speed and high torque. This helps to absorb vibration and reduce chatter during cutting, which is a common problem when machining titanium alloys.
Advantages and Disadvantages of Titanium Machining
Titanium alloy has the advantages of light weight, high strength, good corrosion resistance, etc., so it is widely used in the automobile industry. The most used titanium alloy is in automobile engine systems. The low density of titanium alloy can reduce the inertial mass of moving parts. At the same time, the titanium valve spring can increase free vibration, reduce the vibration of the vehicle body, and increase the engine speed and output power.
Choosing titanium alloy can reduce the load stress of related parts and reduce the size of the parts, thereby reducing the quality of the engine and the entire vehicle. The reduction of the inertial mass of the parts reduces the vibration and noise and improves the performance of the engine. The application of titanium alloy to other parts can improve the comfort of personnel and the beauty of the car. In the application of the automobile industry, titanium alloy has played an inestimable role in energy saving and consumption reduction.
High corrosion resistance, excellent biocompatibility and the best strength-to-weight ratio of all metals. These qualities make titanium alloy a particularly sought-after material in the aerospace and medical industries.
Due to its affinity for other elements, titanium cannot be found naturally, so complex and energy-consuming processes are required to refine it. This means that the price of titanium alloys is much higher than other metals, whether it is the initial smelting of the metal or the subsequent processing.
Another major disadvantage of titanium is the technical difficulty in the machining process.
Related Post: All About Stainless Steel Machining Parts
All About Brass Machining Parts
All About Aluminum Machining Parts