Rapid prototyping is a modern product development method that allows engineers to compress design timelines by iterating faster to reach the final design that can be used in production.
Although 3D printing has become popular as a rapid prototyping method, many industries prefer CNC prototypes to other methods when making models or parts. The applicability of this method depends on the nature of the prototype involved. It is important to consider the purpose of the prototype and the materials of manufacture.
As you will discover, choosing a company that provides CNC prototyping services will bring you great benefits. At SANS Machining, we provide customers with excellent quality prototype processing services.
What Is CNC Prototype Machining?
CNC prototyping involves the use of 3D solid model CAD designs as input, and correspondingly, parts are manufactured directly from solid materials through computer-controlled cutting and milling processes. Some people use the term “subtractive” rapid prototyping to describe this process and compare it to 3D printing (sometimes called “add-on” manufacturing). The subtraction aspect is that the CNC machine removes the material from the starting material block to accurately generate the final part, so as to achieve the CAD model specification. Using modern CNC machines, this material removal process can efficiently, quickly and accurately meet demanding specifications. Due to this subtractive nature, CNC prototypes allow the use of parts made of almost any machinable material. CNC prototype suppliers provide excellent options for small batches of customized products and prototypes, and provide accurate results!
Top Benefits of CNC Machining Prototypes
CNC machining for rapid prototyping can take advantage of the many advantages of computer equipment to produce rapid turnaround prototypes, engineering models and high-quality end-use parts in the shortest time. The following are some of the main reasons to consider CNC machining in your rapid prototyping projects.
1. CNC Machining is fast
With improvements in machines and software applications, it has become one of the fastest and most reliable methods for making complex shapes in metal and rigid plastics.
This speed applies to setup and processing time. First, using modern CAD/CAM design software, three-dimensional parts can be converted into G-code cutting programs, and then transferred to a multi-axis milling machine within a few hours.
Once programmed, a good milling machine or lathe can turn the raw metal blank into a finished product in a few minutes at an amazing speed. Prototype cnc machining will not take a lot of time to give the desired results, even if you wish to use these machines for mass production, you can do it easily without worrying about accuracy, because it can be done even if there is a lot of work Provide higher productivity. In addition, it can produce prototypes that are as close as possible to the original prototype, which is impossible to complete manually. You can set the desired shape and size, and then the machine will be delivered accordingly.
Unlike those who need to rest, CNC machine can run around the clock, 365 days a year. Manufacturers only stop using such machines for maintenance purposes and upgrades.
2. CNC Machining Is Accurate
Through CNC prototyping, a computer program usually in the form of CAD can create a three-dimensional model. After the specifications are entered into the computer of the machine, it will generate the prototype accordingly. The machine follows the commands of the computer software and performs controlled movements to generate accurate models.
In modern mechanical workshops, there is no conventional method with higher precision and precision than computer-controlled cutting tools. This level of accuracy usually produces a tolerance of +0.05mm or 50 microns.

For most commercial applications, this is accurate enough. This is a repeatable tolerance that can be achieved again and again during the production of an unlimited number of parts.
Special cutting tools can be used to obtain tighter tolerances under controlled conditions, such as those that may be required in very demanding aerospace, automotive or scientific applications.
3. CNC Machining Does Not Require Fixed Tools
Some manufacturing processes (such as plastic injection molding or pressure molding) require the use of rigid molds made of hardened or semi-hardened steel alloys. Depending on the complexity of these tools, it can usually take several weeks to make these tools.
The only tool used for CNC milling and turning is the hardened metal cutting insert used in the spindle. Different shapes and types of cutting inserts can perform various cutting functions on the workpiece, but if they are correctly arranged on the automatic turntable, these tools can be swapped out and replaced in a few seconds.
4. CNC machining is easy to modify
You can modify the design very quickly by changing a few lines of G code program. This is particularly attractive for prototyping, as it gives you the opportunity to test several different iterations and immediately evaluate the results. This allows manufacturers to make necessary corrections before going into full production, saving a lot of money. Adjusting procedures and making detailed adjustments “on the fly” can greatly reduce the total delivery time of product development without adding any extra costs.
5. CNC machining can use various materials
Compared with other processes, CNC machining can use a variety of materials. As long as the material is hard enough not to deform or melt under the pressure of the cutting action, the CNC machine will not affect its cutting content. This can also help product development, or when you want to make similar prototypes with slightly different mechanical or appearance characteristics.
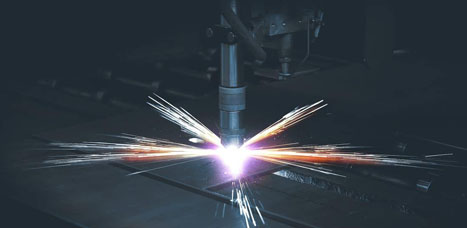
6. CNC machining used in widely application
CNC prototyping can benefit any industry in particular, whether it is aerospace, automotive, construction, aerospace, construction, medical or other industries that require precision and detailed finished products. Investing in the prototyping process through CNC machining reduces the risk of time-consuming and costly errors.
7.Less labor and cost savings
Unlike other machines that require one person to operate each part individually, to obtain results, two people are required at most. One person can handle each part by using related software, and you need another person to configure the machine to produce the necessary design. Human participation is just to deliver instructions, and then the machine completes the rest of the work. The reduced dependence on people will automatically eliminate the possibility of errors due to human interference.
Since there is no need to hire many people, prototype cnc processing can also ensure that business owners do not have to spend a lot of money on wages. In addition, because it can effectively produce a perfect prototype, it can save the cost of modifying the product after it is put on the market. Because of its speed, people can also quickly reach the execution stage, shorten the production cycle and save costs. You only need to spend a small maintenance fee.
We’ve made millions of parts and rapid prototypes, and CNC machining has been a big part of our success. Find out how it can help you when you upload your digital CAD files for a free quotation.