Surface grinding is a finishing process that uses a rotating grinding wheel to smooth the surface of the material, smooth the surface of metal or non-metal materials, and make them look more refined.
The most commonly used abrasive materials for the surface of grinding wheels include: alumina, silicon carbide, diamond, and cubic boron nitride (CBN).
Types Of Surface Grinding
According to the structural characteristics and configuration of surface grinders and worktables, surface grinders can be divided into 4 types, namely, horizontal-spindle reciprocating table surface grinding, Horizotal-spindle rotary table surface grinding, vertical-spindle reciprocating table surface grinding, vertical-spindle rotary table surface grinding.
Horizontal-spindle Reciprocating Table Surface Grinding
The workpiece is sucked or clamped on the worktable by the rectangular electromagnetic worktable, and reciprocating longitudinally. The grinding wheel carriage can make transverse intermittent feed movement along the dovetail guide rail of the sliding seat. The sliding seat can make vertical intermittent feed movement along the guide rail of the column, and the workpiece is ground around the grinding wheel with high grinding accuracy.
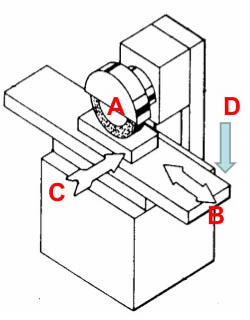
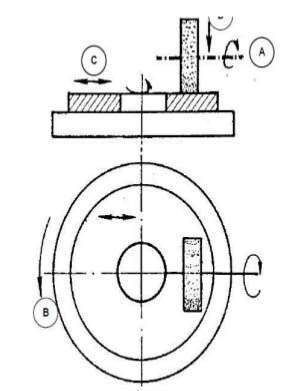
Horizotal-spindle Rotary Table Surface Grinding
The main shaft of the grinding wheel is horizontal, the worktable is a circular electromagnetic chuck, and the surface is ground with the circumferential surface of the grinding wheel. When grinding, the circular electromagnetic chuck sucks the workpiece together and rotates at a uniform speed. In addition to the high-speed rotation, the grinding wheel also reciprocates between the outer edge and the center of the round table to complete the grinding feed. Each reciprocation or each time After reversing, the grinding wheel feeds vertically to the workpiece until the workpiece is ground to the required size. Since the worktable is continuously rotating, the grinding efficiency is high, but it cannot grind complex planes such as stepped surfaces.
It is used to grind round and thin workpieces and can be used to grind annular workpieces with different thicknesses on the worktable.
Vertical-spindle Reciprocating Table Surface Grinding
The main shaft of the grinding wheel is perpendicular to the worktable. The worktable is a rectangular electromagnetic chuck, and the end face of the grinding wheel is used to grind the plane. This type of grinder can only grind simple flat parts. Since the diameter of the grinding wheel is larger than the width of the worktable, the grinding wheel does not need to make a lateral feed movement, so the grinding efficiency is higher.
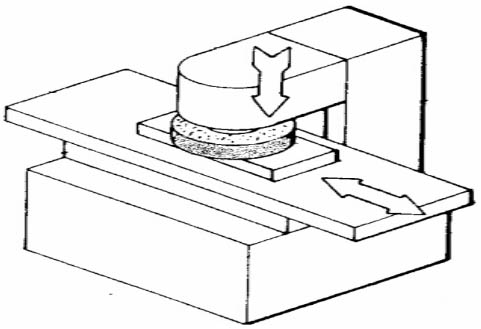
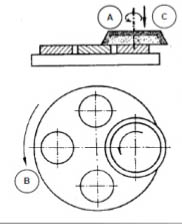
Vertical-spindle Rotary Table Surface Grinding
The main shaft of the grinding wheel is perpendicular to the worktable. The worktable is a circular electromagnetic chuck. The end face of the grinding wheel is used to grind the plane. When grinding, the round worktable rotates at a constant speed, and the grinding wheel rotates at a high speed and feeds vertically. To facilitate the loading and unloading of workpieces, the round table can also be moved longitudinally along the bed rails.
Depending on the working surface of the grinding wheel, surface grinding can be divided into three types: peripheral grinding, end face grinding and peripheral end face grinding.
Peripheral Grinding:
Also known as circumferential grinding, which uses the circumferential surface of the grinding wheel for grinding. Horizontal surface grinders belong to this form.
End Face Grinding:
Grinding with the end face of a grinding wheel. Surface grinders with vertical shafts belong to this form.
Peripheral End Face Grinding:
At the same time, the circumferential surface and the end surface of the grinding wheel are used for grinding. When grinding the step surface, if the step is not deep, you can use a grinding wheel to grind the peripheral end surface on a horizontal axis and rectangular table surface grinder.
Characteristics of surface grinding
The form of surface grinding is different, and its characteristics are also different.
1. Features of peripheral grinding
It can reduce the deformation of the workpiece caused by heating, which is beneficial to improve the grinding accuracy of the workpiece. It is suitable for fine grinding of the plane of various workpieces, the flatness error can be controlled within 0.01~0.02mm/1000mm, and the surface roughness can reach Ra0.8~0.2μm. However, because the intermittent lateral feed is used to complete the grinding of the workpiece surface when it is not grinding, the production efficiency is low.
2. Features of end face grinding
The bending deformation is small, the rigidity is good, and a larger grinding amount can be selected. High production efficiency. The workpiece is prone to thermal deformation and burns. It is only suitable for workpieces with low grinding precision and simple shapes. To improve the quality of end face grinding, the following measures can be adopted:
- Choose a resin bond grinding wheel with coarser particle size and softer hardness.
- Sufficient cutting fluid is supplied during grinding.
- Grinding with insert wheel.
- The end face of the grinding wheel is trimmed into an inner cone center so that the grinding wheel and the workpiece are in line contact or the grinding head is adjusted to a slight angle to reduce the contact between the grinding wheel and the workpiece and improve the heat dissipation conditions.
3. The characteristics of peripheral end face grinding
The grinding amount should not be too large.
Our grinding systems that can achieve surface finishes to 0.2~0.025 Ra with tolerances as tight as 0.002mm. Detailed tolerance and surface finishes can vary due to material type of both the part and the grinding wheel. Contact Us Now