Preface
The industry often says that if we want to realize Industry 4.0, we still have a lot to learn. Among the knowledge to be learned, craftsmanship is the most basic and the first to be understood.
In the entire production process related business of the factory, the process work is in a basic and leading position. If equipment is the muscle of the factory, and sensors and networks are the nerve of the factory, then the craft is the soul of the factory. Therefore, it is imperative to improve the process.
1. The improvement of process work should start with lean optimization of existing processes, implement process standardization, promote process lean, and research process robustness.
Whether it is traditional production methods or smart factories under the industry 4.0 environment, lean and stable manufacturing processes are required. This is also the fundamental way to solve our current efficiency and quality problems.
The so-called “intelligence” of the smart factory is formed by technical personnel who refine a series of judgment factors and thinking logic according to specific business processes, which is not comparable to human intelligence. Therefore, its requirements for manufacturing processes are much higher than traditional production methods. Under the current conditions, imperfect processes will only lead to low production efficiency and unstable product quality. However, in the environment of Industry 4.0, unpredictable errors will occur in unstable process procedures, which will cause the smart factory to cease operation and cause heavy losses.
2. In order to make the process lean and stable, we can no longer use the verification method that relies on actual production.
Instead, we must introduce an important concept of Industry 4.0-Digital Twin, which is to integrate the real environment and state in the virtual digital space. Simulate it to create a virtual digital factory exactly the same as the real factory. The virtual reality environment is used to verify, feedback and improve the process, flow, and planning. Whether it is the details of the processing process or the operation of the macro process layout planning, verification tests can be carried out in the virtual digital factory, which will greatly improve the maturity of the work and save a lot of time and resources.
We have already started to use simulation in technology such as casting, welding, sheet metal, machining, etc., but the current scope of application is small and standardization is not enough. After that, we should formulate a detailed plan, establish a simulation environment, and expand simulation simulation. In the field, the simulation is really effective, and real-time simulation of the whole environment is gradually realized.
3. Change the technological thinking.
All changes originate from the change of thinking. The main work of traditional craftsmen is to compile the process regulations of a single process. In the future, the main work of process technicians will be to refine the logic of process thinking, and constantly supplement, improve and optimize the huge The process database maintains process knowledge data, and the actual process design work may be completed by a computer.
Process procedures will no longer be in the form of a single process, but a discrete process flow of multiple processes. Under the condition of ensuring product quality, the process route is made as flexible as possible so as to provide as much as possible for the decision-making system of the smart factory. Choose and arrange the best route through overall analysis of various influencing factors.
The out-of-date traditional craftsmanship ideas should also be eliminated. The most typical ones are the marking habits of clamping alignment and body tolerance.
In the current production process, the clamping and alignment on the machine tool wastes a lot of machine tool working time, which seriously affects the production efficiency. Due to the continuous improvement of machining accuracy and the increase of machine tool functions, the problem of clamping and alignment can be realized by the precision positioning fixture and the self-aligning function of the machine tool.
The habit of marking the in-body tolerance is because in the past, ordinary machine tools were used to process, in order to reduce the probability of artificial processing out of tolerance and improve the product qualification rate. This makes the actual processing size of the product deviate from the normal distribution, which is not conducive to guarantee Quality stability of bulk products.
At present, CNC machining equipment has been widely used, and the machining accuracy has been greatly improved compared with before. It is no longer necessary to use the in-body tolerance marking for the process dimensions.
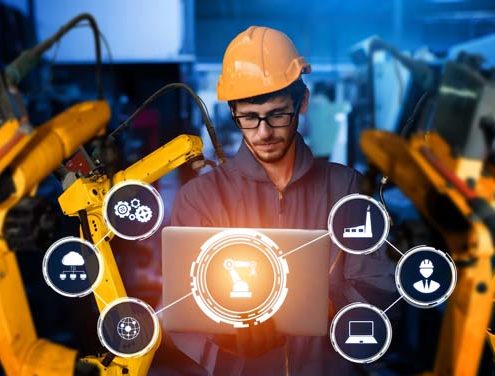
4. Research the application of robots and quick-change fixtures.
The intelligence that Industry 4.0 wants to achieve is not to replace people. Smart factories are not unmanned factories, but to make people and machines work together to achieve higher labor productivity.
For this reason, in smart factories, efforts must be made to eliminate human instability factors. According to the current situation of the manufacturing industry, it is neither realistic nor economical to achieve a high degree of unmanned automated production. The introduction of robots in appropriate links is the best choice to improve stability and efficiency. The use of robots and quick-change fixtures can adapt to the production of multiple varieties and small batches, and improve production efficiency and stability while ensuring flexibility.
5.Integrate the existing process information systems to realize a single data source and ensure interconnection.
Realizing the operation of all businesses under a unified platform is one of the important goals of Industry 4.0. Previously, we invested a lot of resources in informatization construction, especially process informatization. In various businesses, the level of process informatization is relatively high. However, the existing informatization construction lacks overall planning, each information system is relatively independent, and there is no sharing of information resources, forming information islands, which poses a big obstacle to improving the overall business efficiency. Therefore, it is now necessary for us to stand at the level of the company as a whole, integrate the process information system on a unified platform, and truly bring out the role of the information system.
On the road to realize Industry 4.0, we still have a long way to go, and there is still a lot of knowledge to learn, but these are not problems. As long as we seize the opportunity, formulate practical plans, and move forward step by step, In this process, we can improve ourselves, so that Industry 4.0 will get closer and closer to us.
Related Post: How Does Industry 4.0 Affect CNC Machining