When creating a part, one of the most important decisions a design engineer must face is which material to use. The choice of material will determine the function and appearance of a given component and how it will maintain over time.
Plastics are becoming more and more popular. They are light weight, easy to process, and generally cheaper than similar metal products. There are many types of machined plastics, each with its advantages and disadvantages.
There are many ways to produce high-precision plastic parts. Modern industrial grade plastics are cast, injection molded, printed or machined. The first three options are very suitable for manufacturing complex geometrical parts with good surface finish. But when you need to achieve tight tolerances or produce a mirror-like surface finish on almost any type of part, there is nothing better than machining.
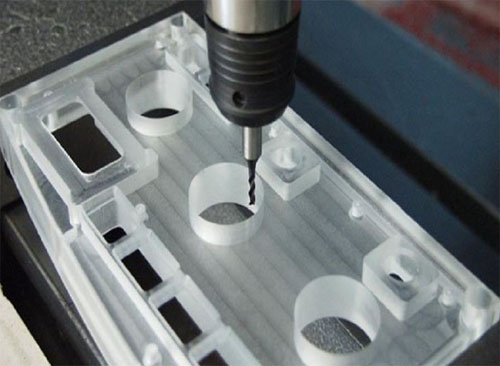
An Overview of Plastic Machining Services
Plastic machining, like all machining processes, is a subtractive method that removes layers of material to shape and form the final part or product. Some of the most common machining operations used for plastic materials are:
Cutting
Usually, the cutting operation generates some heat, which may damage the plastic. When cutting plastic, the operator must take care to avoid thermal deformation.
Turning
Plastic turning operations are performed on a lathe, which rotates and manipulates the workpiece so that the stationary cutting tool can cut and remove excess material according to the intended design.
Milling
The turning operation involves the rotation of the plastic workpiece, while the milling operation requires the rotation of the cutting tool to remove the plastic chips from the fixed workpiece.
Drilling
If the appropriate drill bit is not selected, it may be dangerous and may lead to overheating or shearing forces. However, as long as the preparation is correct and the tools are prepared and used, skilled technicians can form small and large diameter holes in plastic products without destroying the structure.
Grinding
Grinding is similar to grinding because the process removes plastic chips from the workpiece to change its shape. The main difference is that milling uses intermittent cutting, while grinding continuously cuts the plastic from the product to achieve a smoother shape and surface finish.
Materials Used For CNC Plastic Machining
ABS Plastics
Acrylonitrile butadiene styrene, often abbreviated as ABS, is one of the most common thermoplastic materials. It has good mechanical properties, excellent impact strength, high heat resistance and good machinability. ABS is easy to machine, heat resistant and can be used for finishing (glue, paint, polish, etc.). It is usually used to prototype part functions before mass production.
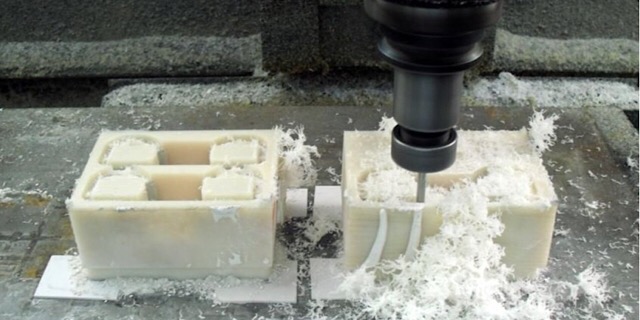
ABS does not have good abrasion resistance or chemical resistance and will melt in acetone. It is also not a particularly strong plastic.
The most common application of ABS is injection molding, which is used to make electronic product housings, household appliances and even iconic Lego bricks.
Nylon
Similar to ABS, nylon is a durable plastic with high strength and rigidity, can maintain good electrical insulation in a wide temperature range, as well as good chemical resistance and abrasion resistance. Nylon 6 and nylon 66 are the most commonly used grades in CNC machining.
But nylon 6/6 easily absorbs moisture, causing it to swell and lose some dimensional accuracy. If a large amount of asymmetric material is removed due to the inherent internal stress of the material during processing, it will also warp.
Nylon is most commonly found in medical equipment, circuit board mounting hardware, automotive engine compartment components, and cable ties. In many of these applications, it is used as an economical substitute for metals.
Acrylic
Acrylic (also known as Perspex or Luctie) is the trade name of PMMA plastic. It is tough, has good impact strength and scratch resistance, and can be easily bonded.
The processed acrylic is transparent, which is very suitable for any application that requires optical transparency or translucency.
However, acrylic is a fragile plastic and will crack or break under too much pressure. Any machined surface on an acrylic board loses transparency and assumes a frosted, translucent appearance. Therefore, it is usually best to pay attention to whether acrylic parts should be left in the original thickness to maintain transparency. If the processed surface needs to be transparent, polishing can be used as an additional post-processing step.
Delrin
POM is well known under the trade name Delrin. It is an engineering thermoplastic with the highest processability among plastics and is considered the most economical plastic. It has a smooth, low-friction surface, excellent dimensional stability and high rigidity. For materials that encounter a lot of friction in these or any other applications, require tight tolerances, or require high stiffness, Delrin is an excellent plastic. But the disadvantage is that it is difficult to bond.
Delrin is usually used for gears, bearings, bushings and fasteners, or to make jigs and fixtures for assembly.
HDPE
HDPE stands for high-density polyethylene, a thermoplastic with a high strength-to-weight ratio. HDPE has high chemical resistance, electrical insulation and durability under severe weather conditions. Similar to Delrin, HDPE has a smooth surface, which can limit friction and resist high impact well, has a high strength-to-weight ratio and good weather resistance.
The main disadvantage of HDPE is its low strength, especially in terms of stretching and bending.
HDPE is a lightweight thermoplastic that is used for outdoor applications and prototyping due to its low cost and light weight. Like ABS, it is often used to create prototypes before injection molding. Due to its chemical resistance and slippery properties, it is very suitable for the manufacture of plugs and seals, and is also ideal for weight-sensitive or electrical sensitive applications.
PEEK
PEEK is a high-performance engineering thermoplastic with excellent impact strength and dimensional stability. PEEK plastic is very easy to process and is the top material used in CNC processing. Because of its amazing performance, it is often used in the automotive, aerospace, medical and electrical industries.
The only drawback is the high price. Nevertheless, if you need high performance and high resistance, you should definitely consider using this material. The performance of this plastic is better than that of metals used in the chemical and processing industries. In some industries, it is currently replacing metals such as stainless steel and aluminum.
Polycarbonite
Polycarbonate is one of the more durable plastics on the market. It has extremely high impact resistance and rigidity, and maintains functionality over a wide temperature range. It is also optically transparent and can be dyed black if opaque is needed. Polycarbonate is best suited for applications that require very tough or very strong plastics or require optical transparency. Therefore, polycarbonate is one of the most commonly used plastics with the highest recycling rate.
Pure polycarbonate does not have good abrasion resistance and is easily scratched. If necessary, an anti-scratch coating and vapor polishing can be added in the post-processing step to improve wear resistance or optical clarity.
The durability and transparency of polycarbonate means it can be used to make optical discs, safety glass, light pipes, and even bulletproof glass.
Tips for CNC Plastic Machining
Machine
There are no plastic CNC machines. In fact, all machine tools used to cut plastics are metalworking tools. Their precise rigidity and power output allow them to easily process even hardened plastics. The rigidity of woodworking machine is low, so the effect is not good.
Cutting Tool
Choosing the best cutting tools for plastic parts is a complex task. The reason for this is that the composition of plastics and composite materials varies greatly. Some plastics are reinforced with hard carbide particles or have additives that enhance flexibility, heat resistance or other parameters. All this changes the way plastics react to machinery.
Cutting tools are mainly made of high-speed steel, cemented carbide, diamond, etc. For cutting ordinary plastics, you can choose the first two cutting materials. In contrast, high-speed steel has better grinding ability. Choose high-speed steel tools and carefully grind them. The cutting edge of the tool will be sharper, but its durability is lower than that of cemented carbide tools.
Reduce the cutting force and temperature as much as possible, select the appropriate rake angle, relief angle, leading angle, secondary cutting edge angle, tool tip arc radius, etc. to improve productivity and tool durability, and save processing costs. The cutter stays sharp and freezes the material when the stiffness is not enough.
Parts Setup
Clamp the plastic block correctly to avoid excessive pressure which may cause rupture. It is recommended to use a pad made of soft material between the fixture and the part to avoid leaving marks on the surface.
Another problem is the rigidity of the parts. You need to pay close attention to the distance between the drilling location and the fixture. During this process, the drill bit will try to pull the part up along its groove. If the fixture is too far away, the drill bit will succeed, but it will bend the part or may actually tear the part from the fixture.
Minimize the Chip Effect
Always keep the cutting tool moving (avoid staying in one place for too long) to prevent the chips from melting onto the processed parts. Coolant or cutting fluid can be used to lower the temperature and remove chips.
Machining Feed
Using a larger feed rate and fast spindle speed, it is about 3 times the aluminum feed and the corresponding cutting speed.
CNC Plastic Machining Service
Due to the large demand for plastic parts for prototype manufacturing and customized CNC plastic parts, a large number of CNC plastic machining services have emerged. They undoubtedly make the production process of all parties faster and easier. If you have related projects, welcome to upload drawings to get free quotation from SANS Machining.