What is precision machining, small and exquisite, no matter from the material and craftsmanship, it is made with very careful craftsmanship. It is by no means batch-produced parts, but also a kind of mechanical processing. For precision parts, processing is very strict. The precision of parts also represents one of the foundations of the competitiveness of an enterprise. The workpiece processing requirements in precision machining generally use the form of CNC for precision machining of parts.
When performing precision processing, the mechanical processing plant not only meets the customer’s workpiece processing technical requirements, but also has the required performance, and should pay attention to the improvement of production efficiency and worker efficiency, so as to provide customers with more economical and long-term effective services. So let SANS explain to you what is the general processing operation of high-precision parts.
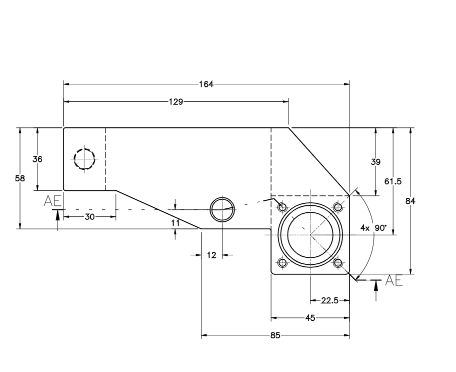
1 Check customer drawings and select suitable machine tools
First of all, after receiving the customer’s drawing processing requirements, before starting the precision machining, it is necessary to select the appropriate CNC machine tool and write several sets of economical and profitable processing procedures. Appearances that require high mechanical processing quality are divided into processing stages, which can generally be divided into three stages: rough processing, semi-finishing and finishing. Mainly to ensure the processing quality, facilitate the scientific application of equipment, facilitate the arrangement of the heat treatment process, and to facilitate the discovery of blank defects.
2 Customize reasonable CNC machining plan
Then formulate a suitable CNC/mechanical processing plan for precision parts, analyze the drawings of the parts to be processed, perform parts on the processing content of the parts and adopt appropriate processing techniques.
CNC high-speed precision parts processing process:
- Product analysis: certain composition information and some specific processing requirements should be obtained through product analysis.
- Graphic design: Graphic design should first be based on a detailed analysis of the product. For example, for stamp processing, we must analyze the processing requirements to determine the font, text size, stamp type, etc.
- Process planning: Through the analysis of the appearance and processing requirements of the workpiece product in the early stage, each processing step is established reasonably from the overall processing.
- Path generation: The process of path generation is actually that we implement process planning through software, and at the same time, we optimize the tool path to a certain extent through parameter settings.
- Path simulation: After the path is generated, we generally have no intuitive feeling about its final performance on the machine tool. Here we can check the possible problems through path simulation, thereby reducing the scrap rate of actual processing. The general inspection focuses on the appearance of the workpiece, whether it is over-cut or under-cut, and then whether the process planning of the path is reasonable.
- Path output: Path output is a necessary step for software design and programming to be realized on the machine tool. Through path output, an intermediate reference can be used to establish a connection between the two. If the students have a professional background in CNC, it can also be understood as the post-processing of the tool path.
3 Choose a material with appropriate hardness
Secondly, the choice of material hardness. For some occasions, the higher the hardness of the material, the better, but it is limited to the hardness requirements of the machined parts. The material is moderately soft and hard, at least a grade lower than the hardness of the machine parts. Therefore, the most basic One is to pay attention to the density of the material before processing.
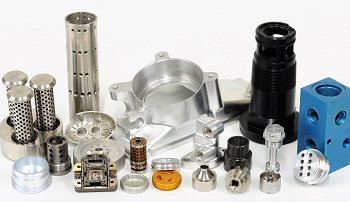
4 Determine the process programming
Then in the processing of high-precision parts, it is important to write and design the process flow, because the process steps of the part processing, the selection of benchmarks, the selection of processing tools, the selection and installation of fixtures, and the determination of processing strategies and process parameters affect The quality of the product.
5 Check product quality
Finally, in the process of high-precision parts processing, we must also pay attention to the full inspection of product quality before arranging shipments. If it does not conform to the drawings, the secondary processing will meet the dimensions, accuracy, tolerances, technical parameters and other requirements of the drawings. Dalian SANS has a complete range of precision machining equipment, CNC machine tools, and testing equipment. It has more than ten years of precision machining experience. It strictly controls product quality and can provide a one-stop service that saves effort and effort.