The use of plating for surface treatment on many metal machinery and parts has many well-known benefits. The plating helps protect the part from wear and corrosion damage, improve the performance of the part or part, and even increase/decrease the electrical conductivity of the part.
Electroless nickel plating and hard chrome plating are two common surface treatments. Which is better has become a topic of debate among manufacturers. Therefore, here are some facts to help you better understand the difference between the two finishes. We will focus on the detailed introduction and comparison for each plating method.
Definition For Hard Chrome Plating And Electroless Nickel Plating
What is hard chrome plating?
Chrome plating is the process of applying a chromium layer to a metal object. The first step in the industrial chromium plating process is usually to degrease and clean the surface to which chromium will be applied, which is called the substrate. Depending on its composition, the component may also require other types of pre-processing. The electroplating expert will then lower it into the electrochemical bath until the desired thickness is reached.
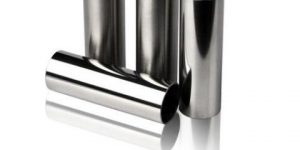
Hard chrome (often called industrial chrome) differs from decorative chrome in that its main purpose is function rather than aesthetics. The main purpose of decorative chrome is to enhance the visual appeal of objects by applying a thin chrome coating. Hard chrome plating is more durable in a wide range of uses and environments.
Application about hard chrome plating.
The definition of hard chromium plating is an industrial chromium used to complete the functionalization of parts. There is also a decorative chrome finish which is more aesthetic and can be used for the visual appeal of motorcycles and cars. Although hard chrome is inherently decorative, it is more suitable for engineering applications than the more common decorative chrome finishes. Some of these applications are machine tools, sometimes hard chrome plated to extend the life of the tool. Because hard chromium also has anti-sticking and anti-sticking capabilities, hard chromium plating is often used on gears and plastic molds. These characteristics also make hard chrome the preferred finish for pistons and shock absorbers of various machines and vehicles.
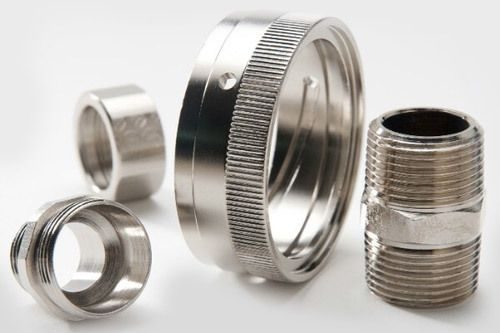
What is electroless nickel plating?
The electroless nickel plating process uses a nickel-phosphorus alloy to coat the substrate. This will protect it and improve its function. As the name suggests, electroless nickel plating does not require electric current like hard chrome plating. On the contrary, after cleaning, pre-treating and activating the substrate, the nickel plating technique uses an autocatalytic chemical reaction to deposit the coating.
In the electroless nickel plating process, hypophosphite is used as a reducing agent, resulting in various amounts of phosphorus in the coating. Electroless nickel is classified as having low, medium or high levels of phosphorus. The phosphorus content of the low-phosphorus coating is about 2% to 5%. The intermediate level is about 6-9%, and the advanced level is about 10% to 13%. The most typical is the medium coating, the phosphorus content is about 8%.
The phosphorus content in the coating will affect its properties. Low-phosphorus coatings can provide the hardest coating, medium-hard coatings have lower hardness, but the fastest coating, while high-phosphorus coatings have the lowest hardness but the best anti-corrosion effect. All coatings can be baked to increase hardness, but this will reduce corrosion resistance.
Application about hard chrome plating
Electroless nickel plating is used for various parts in many industries including automotive, electronics and petroleum industries.
Automobile manufacturers use it to protect parts such as pistons, injectors and cylinders from wear and corrosion. For similar reasons, the aerospace industry uses it on valves, engine shafts and other components.
The oil and gas industry uses electroless nickel plating on equipment that faces harsh underground or underwater conditions. This is a key part of various pumps and pipe fittings.
It is also common to find nickel plating in electronic products such as hard disk drives and printed circuit boards. Like hard chrome plating, it can be used in molds to improve demoulding and anti-sticking capabilities, and to restore worn or damaged parts. This is also a commonly used coating on packaging and handling machinery.
What are the similarities between electroless nickel plating and hard chrome plating?
Both electroless nickel and hard chromium plating are suitable for various substrates, because the electroplating process will be uniformly deposited on all surfaces of the parts to be polished, which is very suitable for electroplating irregularly shaped objects and objects with holes and dents. Both can also cover many different materials, including stainless steel, copper, brass, etc. (even including some plastics). Both hard chromium and chemical nickel are very durable and can be used for a long time even under constant mechanical contact. Both also have excellent corrosion resistance, and due to the sliding properties of the two surface treatments, the friction coefficient is significantly reduced. Finally, hard chrome or electroless nickel plating is usually used to improve the appearance of the components.
What are the differences between Hard Chrome & Electroless Nickel Plating?
Durability
Hard chrome and electroless nickel plating are popular because they dominate in durability. Due to its extremely high hardness, hard chromium is slightly more durable than nickel. It usually wears less and is best suited for high friction conditions.
The electroless plating process makes nickel in the plating layer persistent. Nickel applied by conventional electrolysis methods will change color in a relatively short time. However, chemical nickel has a longer service life and does not degrade, which makes it a more economical choice.
Corrosion resistance
One of the most important advantages of metal plating is that it has abrasion resistance and also has abrasion resistance. Both hard chromium and chemical nickel can resist corrosion and protect the material from degradation caused by contact with the environment.
Although both coating materials have suitable corrosion resistance, studies have shown that electroless nickel plating performs well in this field, especially in blind holes. These holes are more difficult to plate and are prone to corrosion. Electroless nickel plating can form a more uniform coating in these hard-to-reach places, thereby more effectively preventing corrosion in these areas. Both are good choices, but if corrosion resistance is a priority, electroless nickel plating may be used.
Hardness
As the name suggests, hard chrome is known for its hardness. This feature helps it to withstand the abrasion of industrial applications including severe mechanical contact. After electroplating, its Rockwell C hardness is between 68 and 72.
Chemical nickel can also protect components from long-term wear and tear, which helps to make parts longer life and save the company maintenance and replacement costs. After electroplating, the Rockwell hardness of this material is 63.
If you put abrasion resistance first, you can choose to use hard chrome. However, both chromium and chemical nickel can protect equipment and parts from wear.
Appearance
Although appearance is not usually the main consideration for industrial use, another benefit of choosing hard chrome plating or electroless nickel plating is to provide a glossy, smooth and modern appearance.
The color of nickel is another classic look that you can see in most fixtures in most houses. The appearance of electroless nickel plating is smoother than that of electrolytic plating, and unlike more conventional nickel, the yellowish tint of electroless plating will fade over time.
Hard chrome coatings usually need to be polished in certain areas to provide more uniform coverage. Therefore, this makes electroless nickel plating an ideal surface treatment with dents, holes and irregularities.
What to Consider and How to Choose
When you need to choose between hard chrome plating and electroless nickel plating, you may face a difficult decision. Both are useful, but the correct choice depends on how you plan to use plated components. When weighing options, the following points should be considered.
Wear
Will the use of this component wear out over time? The possibility of part wear is affected by the frequency of use and other objects in contact with it.
If you need the coating to be very hard and durable, use hard chrome. For parts that face a lot of possibility of wear, hard chrome is the best choice for parts that can work normally and can be used for a long time even under severe conditions.
Environment
Under what conditions will you use the component? Consider whether to expose it to damp, hot or cold environments.
If you are most concerned about corrosion, electroless nickel plating should be your preferred electroplating material. The uniformity and smoothness of the coating leaves no space for moisture and other elements to pass through, thereby protecting your components and helping them to work better and last longer.
Motion
Is the part a moving part that needs to run smoothly without wear? Jammed parts may slow down or stop the process and damage the equipment.
If the parts you want to plate are moving parts, please choose hard chrome. Its coefficient of friction is very low, which means things move more easily along it. It also retains oil well, thereby improving performance.
The shape of the substrate
Is the shape of the object to be plated relatively smooth and uniform, or is it irregular? Check for holes, dents, irregular parts and rough surfaces.
The uniformity of chemical nickel enhances its corrosion resistance and also makes it very suitable for coating irregularly shaped items. If the surface of the component is rough, has holes and other areas that are difficult to cover, please use this material to ensure that every inch of the device is protected.
In short, as with most comparisons of advantages and disadvantages, it actually really depends on the specific purpose of the end-use application and component. Even in the case of hard chromium plating that provides better hardness and lower coefficient of friction, electroless nickel plating may be better accepted because of its better all-inclusive surface quality.