Aluminum anodization is an electrochemical process that transforms the aluminum surface into a decorative, durable, corrosion-resistant and wear-resistant oxide layer. The alumina is not applied to the surface like coating or electroplating, but is completely integrated with the underlying aluminum substrate.
The anodized aluminum part is not easy to chip or peel off, and has a highly ordered porous structure, which can be subjected to secondary processing such as coloring. The color of anodized aluminum can meet the various color needs of customers and can be customized according to the Pantone color number. (More at: All About Machining Anodized Aluminum Parts)
Electrolytic colored oxide film and hard oxide film have been widely used in our lives, so today we will focus on analyzing the factors that affect the cost, coloring and quality of anodized aluminum parts.
Factors Affecting the Anodizing Aluminum Part Cost
Regarding the cost of anodized aluminum parts, although it depends on different requirements, there are three key factors that affect the cost of anodized aluminum parts. The cost of anodized aluminum mainly depends on the thickness of the coating, the size and shape of the parts, and the additional services required.
Coating Thickness
If the type of coating does not require a specific thickness, it is considered a “basic” coating and has the lowest price.
Controlling the precise coating thickness will affect the cost. If the coating thickness specification includes upper and lower limits, the narrower the range, the higher the cost. For example, the price of +/-.001″ is cheaper than the stricter range of +/-.0001″. The maximum coating thickness may cost more because they require longer production times.
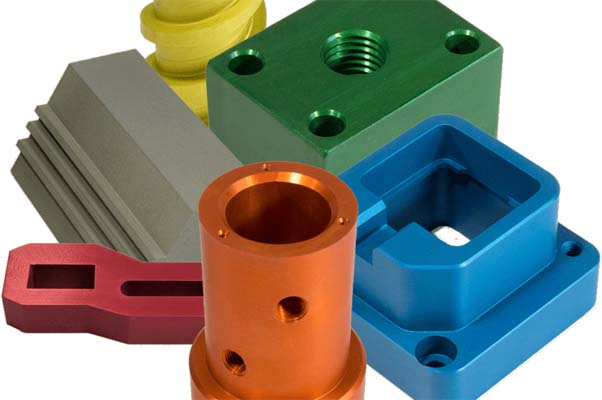
Rack
The rack is critical to quality. Aluminum or commercial pure titanium racks will be used to make electrical contacts. If the job does not specify shelf requirements, the manufacturer will use the most cost-effective method to obtain the highest yield. Special shelf requirements may limit the number of parts processed at one time, and the cost of each part may rise.
The number of parts anodized at one time is affected by power supply limitations. Anodizing is performed at 15 or 30 amperes per square foot (ASF). Therefore, the maximum surface area can be processed in each run.
Additional Services
Customers usually need other processes to increase the anodizing process. These services will increase labor and time when parts require simple or complex covering or punching. These services add value, but also increase the total cost of anodized aluminum.
Factors Affecting the Anodizing Aluminum Part Color
Impurities In Electrolyte
The coloring degree of aluminum alloy products mainly depends on the formation quality of the anode layer. Therefore, impurities have a great influence on the oxide film in the sulfuric acid oxidation solution. Impurities are mainly metal ions, such as copper, iron, aluminum and organic impurities.
Copper Ions
The copper ions will be replaced and deposited on the surface of the aluminum part, resulting in a reduction in the porosity of the anode layer and reducing transparency, corrosion resistance and electrical insulation properties. Therefore, the content of copper ions cannot exceed 0.02g/L.
Chloride Ions
Chloride ions come from tap water or cooling water. The content of chloride ions should be less than 0.2g/L. Otherwise, the anode layer will be rough and loose, which will corrode the surface of aluminum parts (breakdown) in severe cases.
Aluminum Lons
The aluminum ions in the electrolyte gradually increase. When the content is greater than 25g/L, the conductivity of the electrolyte decreases, and the surface of the workpiece shows white spots or blocky white spots, and the adsorption capacity of the film decreases, causing difficulty in coloring.
Iron Ions
The iron ions in the electrolyte should not exceed 0.2g/L, otherwise dark stripes and spots will appear.
Organic Impurities
Organic impurities hinder the formation of the anode layer. After this layer absorbs oil, it causes uneven color and spots.
Remove Grease
We need to thoroughly remove the oil stains before the parts are colored to avoid obvious white spots on the film layer, otherwise it will make the coloring difficult.
Electrolyte Concentration
When the tin salt concentration in the electrolyte is too low, the coloring speed is slow. When the concentration is higher than 25g/l, the coloring speed is fast, but it is not easy to grasp, and the color difference is often large.
Coloring temperature
The coloring temperature also has a great influence on the coloring effect. For example, the normal coloring temperature is 15°C. When the temperature is lower than 15°C, the coloring will slow down, but when the temperature is too high, a layer of mist will appear on the surface of the oxide film, which will cause the bath to become turbid.
Color time
It will directly affect the quality and color resistance of aluminum alloy parts: the coloring time is short and the color is easy to fade. The longer the time, the darker the color and gloss, and the surface is easily scratched.
Coloring voltage
When the coloring voltage is low, the coloring is slow, the color change is also slow, and uneven color tone is likely to occur. When the coloring voltage is high, the coloring speed is fast and the colored film is easily peeled off.
Other factors
Whether in anodizing or electrolytic coloring, surfactant-based additives and stabilizers should be added to stabilize the formation speed and thickness of the layer, inhibit the dissolution of the anode layer and improve the color uniformity.
In addition, the pH value, water quality, and coloring tank materials have a certain impact on the coloring quality. Only by ensuring that the parameters are within the control range can the quality of the electrolytic coloring anode layer be guaranteed.
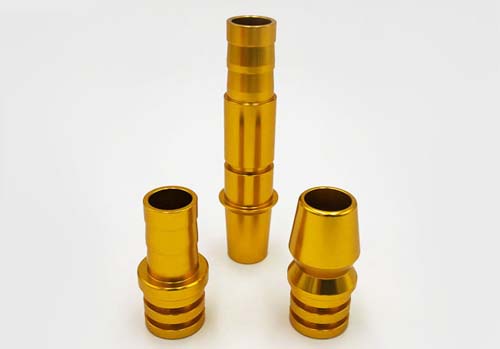
Factors Affecting the Anodizing Aluminum Part Quality
Sourcing materials
The aluminum alloy itself can determine the final effect of anodizing from multiple angles. Each compound has an alternative structure of alloy composition, some of which are particularly effective in anodizing, while others are not. For example, 6061 aluminum has become one of the most popular alloys chosen by machining plants and manufacturers for its quality, surface integrity, protection from environmental conditions, and workability.
After selecting the right alloy, similar parts must be used as much as possible throughout the activity. There may be multiple types in the supplier’s inventory. The supplier’s inventory quality (primary inventory and secondary inventory) and its production or discharge method will greatly affect the final product after anodization.
Surface Treatment
Anodizing is not like other finishing processes at all, because it will find aluminum substrates during the preparation process, which is very similar to thin film improvements. Therefore, it is necessary to consider sending each part of the aluminum surface ready for anodization. Legal treatment and maintenance of aluminum components in the processing workshop will ensure predictable results during the anodizing process.
Chemistry Is Essential
One of the most basic parts of obtaining high-quality and reliable results in the anodizing process is to strictly control the scientific nature of each cell. The method of anodizing has many steps, including: cleaning, pretreatment (etching), anodizing, shading (except for transparency), sealing, and obviously there are various rinses in the middle of each step.
The control measures that must be maintained for each method are: pH, concentration, temperature and time. The chemical supplier does specify the parameter range for each substance, but it is important for each anodizer to conduct its own special research and testing to find the ideal range. This should be possible with the help of chemical management software and consultations provided to chemical suppliers.
Anodizing Tank Control
True anodizing technology requires maintaining various controls on the tank itself and has a specific ultimate goal to ensure a stable, high-quality coating. In addition to the chemicals in the tank (currently specified), regular adjustments to the power supply (rectifier) are essential.
The anodizing time, temperature, stirring and cathode quality in the tank may also become the most important factors and will affect the final aftereffect of the coating on the part during the anodizing process.
Get reliable products engineered to high standards of quality! SANS is a CNC manufacturing and metal part fabrication company, including CNC machining services, CNC milling services, CNC turning services, EDM services and parts assembly services. Email us info@sansmachining.com for free quotation for your projects.