There are many ways to change the properties of metals and their response to precision machining. One of these methods is heat treatment. Heat treatment affects many different aspects of metals, including strength, hardness, toughness, workability, formability, ductility and elasticity. It also affects the physical and mechanical properties of the metal, thereby changing the use of the metal or changing the future work of the metal. These changes occur due to changes in the microstructure and sometimes chemical composition of the material
Here, we carefully study the most commonly used metal alloy-related heat treatments in CNC machining and how these heat treatments affect parts in precision machining.
What Is Heat Treatment?
Many standard CNC production facilities use heat treatment. Manufacturers can change the strength, plasticity and corrosion resistance of finished components by choosing to include heat treatment processes.
These treatments involve heating the metal alloy to a (usually) extreme temperature and then cooling under controlled conditions to change the physical state or mechanical properties of the material. The temperature to which the material is heated, the time to maintain this temperature, and the cooling rate greatly affect the final physical properties of the metal alloy.
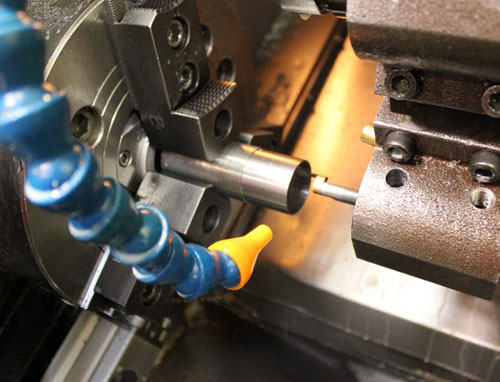
Part of the design and engineering process is to determine what physical properties are required for the part, and to select the best metal to meet these requirements. Heat treatment of metal alloys before or after processing can greatly improve key physical properties. Heat treatment increases the hardness, strength or workability of the metal.
Types of Heat Treating
Annealing
Annealing is a heat treatment process through which the material is heated to a critical temperature and then slowly cooled. The annealing process changes the physical structure of the material, making it softer and more ductile.
Annealing is a heat treatment method in which a metal such as aluminum, copper, steel, silver, or brass is heated to a specific temperature and maintained at that temperature for a period of time to undergo transformation, and then air-cooled. This process increases the ductility of the metal and reduces the hardness, making the metal easier to process. Copper, silver, and brass can be cooled quickly or slowly, while ferrous metals like steel must always be gradually cooled for annealing to occur.
Annealing is usually carried out after all metal alloys are formed and before further processing to soften them and improve their workability, so that harder materials are not easily cracked or broken. If no other heat treatment is specified, most CNC machined parts will have material properties in the annealed state.
Tempering
Tempering also heats parts at a temperature lower than annealing, usually after quenching mild steel (1045 and A36) and alloy steel (4140 and 4240). Tempering can be used to change the hardness, ductility and strength of metals, which usually makes them easier to process. The metal will be heated to a temperature below the critical point because the lower temperature reduces brittleness while maintaining hardness.
Stress relieving
Stress relief involves heating the part to a high temperature (but lower than annealing), and then slowly cooling the part. It is usually used after CNC machining to eliminate the residual stress generated during the manufacturing process. In this way, parts with more consistent mechanical properties can be produced.
The elimination of stress is a necessary condition to eliminate the internal stress of the material in the previous manufacturing process. If there is no stress relief, the parts will crack or lose tolerance during use, which will eventually lead to parts damage.
Quenching
Quenching involves heating the metal to a very high temperature and then performing a rapid cooling step. Usually the material is immersed in oil or water or exposed to a stream of cold air. However, depending on the final mechanical properties required by the part, polymers or salts are sometimes used . Rapid cooling “locks in” the microstructural changes that the material undergoes when heated, resulting in very high hardness of the part.
Parts are usually quenched after CNC machining as the last step in the manufacturing process to achieve high surface hardness. The tempering process can then be used to control the resulting hardness. For example, the hardness of tool steel A2 after quenching is 63-65 HRC, but it can be tempered to a hardness between 42 and 62 HRC. Tempering can reduce the brittleness of the parts, thereby extending the service life of the parts (the hardness is 56-58 HRC for best results).
Case Hardening
Case hardening is a series of heat treatments that can result in high surface hardness of parts while maintaining softness inside the material. This is usually better than adding hardness to the entire volume of the part (for example by quenching), because harder parts are also more brittle.
Carburizing is the most common case hardening heat treatment. For metals with low carbon content (such as steel), additional carbon must be injected into the surface, and then the part is quenched to lock the carbon in the metal matrix, which increases the surface hardness of the steel in a manner similar to the way anodizing increases the surface hardness of aluminum alloys .
Case hardening is a process usually used as the last step after the part has been machined. Combine high heat with other elements and chemicals to produce a hardened outer layer. Because hardening makes metals more brittle, surface hardening is useful for applications that require flexible metals with durable wear layers.
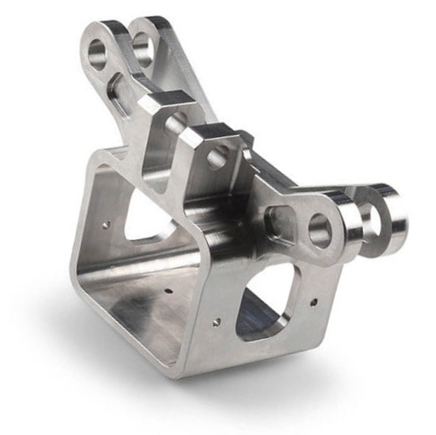
When Are Heat Treatments Applied?
The metal alloy can be heat treated throughout the manufacturing process. For CNC machining parts, the following heat treatments are usually used:
Before CNC machining: If required to provide a standardized grade of metal alloy, the CNC service provider will directly process the parts from the stock material. This is usually the best option to reduce delivery time.
After CNC machining: Certain heat treatments can significantly increase the hardness of the material, or used as a finishing step after forming. In these cases, high hardness will reduce the machinability of the material, so heat treatment is performed after CNC machining. For example, this is the standard practice when CNC machining tool steel parts.
How to specify a heat treatment in your order
When placing a CNC order, there are three ways to request heat treatment:
Give a reference to manufacturing standards:
Many heat treatments have been standardized and widely used. For example, the T6 indicator in aluminum alloys (6061-T6, 7075-T6, etc.) indicates that the material has been precipitation hardened.
Specify the required hardness:
This is a common method for specifying heat treatment and surface hardening of tool steels. This will indicate to the manufacturer which heat treatment he needs to perform after CNC machining. For example, for D2 tool steel, the hardness is usually 56-58 HRC.
Specify heat treatment cycle:
This requires advanced metallurgical knowledge. If you understand how different heat treatments affect metals, you can specify the required heat treatment process so that you can specifically modify the material properties of the application.