CNC加工は今でも金属切削加工の範疇にありますが、独自の特徴があります。 これは主に高度な自動化、長時間の連続加工プロセスとして実現されており、工具の設定にかかる時間は従来の加工よりも複雑で時間がかかります。 したがって、ツールの選択では、検討する価値のある多くの質問があります。 この記事では、CNCで一般的に使用されるツールの関連知識を紹介します。 良い工具はCNC加工の効率を上げるための第一歩だと思います。
工具材料とコーティング
現在使用されているさまざまな工具材料には、さまざまな加工要件に適合する特性があります。 一般的な工具材料に必要な特性には、低摩擦係数、高精度、優れた熱伝導率、十分な靭性、耐衝撃性などがあります。
従来のCNC工作機械の一般的な工具材料は、高速度鋼と超硬合金です。 ただし、高速切削、乾式切削、機械加工が難しい材料の切削、研削の代わりの旋削などの特別な場合には、セラミック、CBN、PCBN、ダイヤモンドなどの超硬材料を使用する必要があります。 これらの超硬材料は価格が比較的高く、切削工程やパラメータの習得が容易ではなく、工作機械の剛性に一定の要件があり、従来の加工にはあまり応用されていません。
超硬材料ツール
工具表面コーティングは、工具性能を向上させるための重要な方法の1つであり、近年広く使用されています。 コーティングありの工具寿命は、コーティングなしの工具の10倍です。 一般的なコーティングには、窒化チタンTIN、炭化チタン窒化物TICN、および酸化アルミニウムが含まれます。 次の図は、高速度鋼と超硬合金の切削速度が100分の1に短縮され、コーティングされた工具の使用により処理時間が4分の1に短縮されたことを示しています。
ツールの分類
一般的に使用されるCNC工具は、その形状に応じて、エンドミル、ラウンドノーズカッター、ボールカッターの3種類に分類されます。 各ツールには固有の役割があります。
エンドミル
CNCマシニングセンターのエンドミルは平底カッターとも呼ばれ、主要な刃先に囲まれ、底部はマイナーな刃先です。 エンドミルの外縁と底面には刃先を形成するためのフライス歯があり、ワークの垂直面をフライス盤で削ることができます。 エンドミルの形状変化は非常に複雑で、フライス盤、溝、輪郭面などあらゆる加工に適しています。 最も広く使われているフライスと言えます。
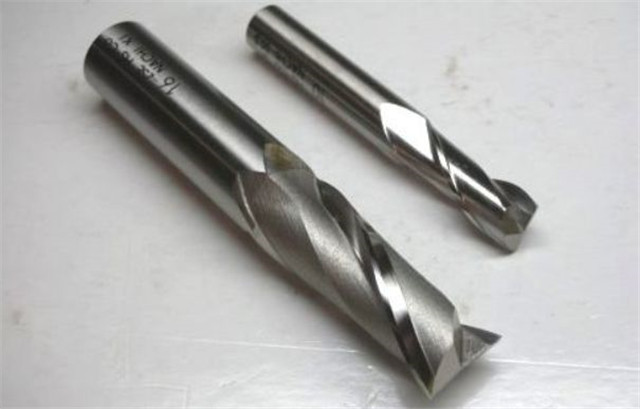
2D形状のワークをフライス盤加工する場合、ワークと接触する部分が外縁と底面であるため、工具ピッチと切削深さの両方に非常に効率的な値を使用することができます。 ただし、3Dワークの金型を切削する場合、ワークとの接触面積はほとんどの場合鋭い点に近くなります。 そのため、工具間の距離や切り込みを小さくする必要があり、加工効率が低下します。
つまり、エンドミルは2D形状のワークピースには適していますが、3D形状のワークピースには適していません。
ボールナイフ
底刃がボール型の刃は、Rナイフとも呼ばれるボールナイフです。 エンドミルとは対照的に、ボールカッターは3Dワークピースのフライス盤に不可欠なツールです。 ボールナイフの底にはエンドミルのような鋭利な先端がなく、R角の刃があるため、ボールナイフの刃はより安定しており、つぶれにくいです。
金型加工では、ボールカッターは主に3D金型のフライス盤、特に仕上げとコーナークリーニングに使用されます。 ただし、球面カッターとワークの接触面積が小さく、距離を伸ばすことができないため、比較的平坦な領域のフライス盤には適していません。
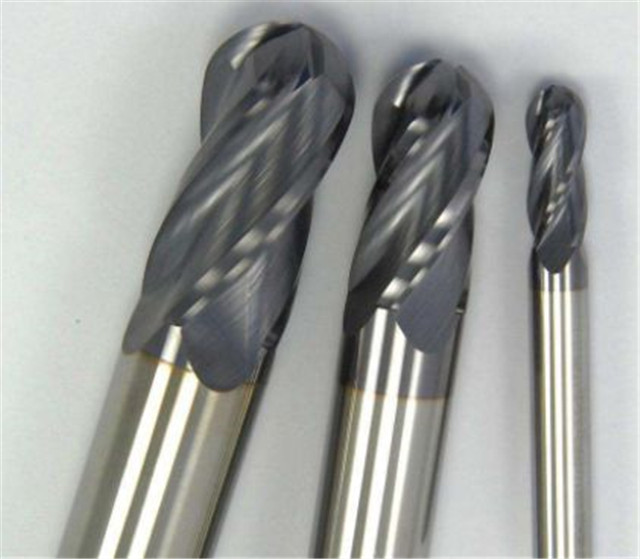
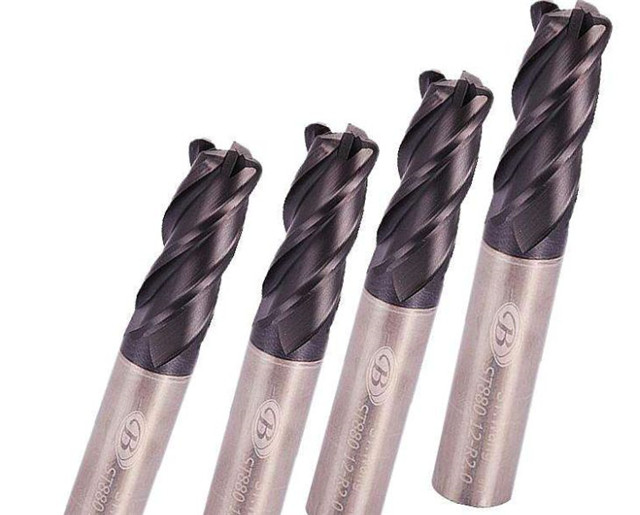
ラウンドノーズナイフ
CNCマシニングセンターのラウンドノーズナイフは平底Rナイフとも呼ばれ、荒削り、フラットスムースナイフ、曲面コンタースムースナイフに使用できます。 エンドミルや球面カッターと比較して、ラウンドノーズカッターは2つの利点を組み合わせており、作業効率が優れています。 ラウンドノーズナイフの水平ナイフ間隔はボールナイフよりも大きくすることができ、仕上げ時のボールナイフと同じ利点があります。 したがって、ラウンドノーズナイフは荒削りや仕上げに適しています。
ワークが大きく、表面変化が小さく、凹みの狭い領域が小さく、比較的平坦な領域が大きい場合は、丸刃ナイフを使用して処理するのが最適です。 次に、二次荒削り法を使用して、後続の処理が必要な領域を見つけます。 しかし、いくつかのくぼんだ領域に面して、丸い鼻のナイフは刃のブラインド領域を持っており、「上端」の現象が見られます。
一般的な問題と解決策
実際の運用では、常にさまざまな問題が発生します。 ここに、すべての人に共通する問題と解決策がいくつかあります。 これらの問題が解決されることで、工作機械の加工効率が向上すると思います。
ツールの振動
加工が難しい材料の使用が増えるにつれ、振動が加工効率向上の障害となっています。 振動の発生は、加工精度や表面粗さに直接影響し、工具摩耗を加速し、工具寿命に深刻な影響を及ぼし、深刻な場合には切削作業を継続できません。
工具の振動には、同時に存在する3つの条件が必要です。 ツールを含むプロセスシステムは十分に剛性が高くないため、固有振動数が低くなります。 切削時に十分な大きさの外部加振力が発生します。 外部加振力の周波数は、プロセスシステムの固有周波数と同じです。 共振。
ツールの振動を解決するという考え方は、3つの部分に分かれています。 1つ目は、切削抵抗を最小限に抑えることです。 切削抵抗を減らすには、可能な限り最小のチップアークを使用します。 工具のすくい角を大きくします。 プレスされたブレードをグラウンドブレードと交換します。 切り込みの深さを減らし、速度を上げ、送りを増やします。 細長いシャフトには90度の進入角度を使用してください。 細いロッドを備えたフライス盤の場合、丸いインサートが振動の低減に最も役立ちます。
2つ目は、ツールシステムまたはフィクスチャとワークピースの静的剛性を最大化することです。
3つ目は、ツールバーの内部に別の振動を発生させて、外部から励起された切削抵抗の振動周波数を乱し、それによって工具の振動を排除することです。
ブレードウェア
機械加工プロセス中に、前面と背面の工具面がすぐに摩耗することがよくあります。 その中で、ブレードの損傷条件に応じて、さまざまな対応方法が必要です。
1.逃げ面の過度の摩耗は、粗い表面と不十分な加工寸法につながります
このシナリオの理由には、切断速度が速い、またはブレードの耐摩耗性が低いなどがあります。 解決策としては、切削速度を落とす方法を改善し、切削量を徐々に増やし、耐摩耗性の高いブレード材料またはコーティングを使用し、アップミリングではなくダウンミリングを使用することを試みます。
2.ノッチ摩耗
刃の溝を削った後、損傷して表面粗さや欠けの原因となることがあります。 理由には、送り速度が小さすぎることが含まれます。 フライス盤は加工硬化する傾向があります。 ワークの表面に酸化物スケールなどがあります。 このような状況に直面した場合、ブレードの溝の摩耗を釘で頻繁にチェックする必要があります。
3.ステンレス鋼と耐熱合金をフライス盤するときの構成刃先
フライス盤の粘着カッターは構成刃とも呼ばれ、加工面が粗くてバリになります。 構成刃先の脱落により、刃のすくい面が脱落し、刃先がつぶれ、耐熱合金加工物の二次欠けにより、刃先が急速につぶれます。 このような状況の理由は、刃先が鈍い、すくい角が負である、切削速度が遅い、切りくずの厚さが薄すぎる、切りくずの除去が不十分であることに他なりません。
蓄積した腫瘍を解決する方法は、大まかに「6つのステップ」に基づいています。 最初のステップは、ステンレス鋼とアルミニウム合金の切削速度を上げることです。 2番目のステップは、物理的にコーティングされたブレードまたはコーティングされていないブレードを使用することです。 3番目のステップは、最適な切りくず厚さを実現するために、切削量を徐々に増やすことです。 4番目のステップは、二次切りくずを防ぐのに十分な高圧クーラントまたは空気を準備します。 5番目のステップは、アップカットミリングの代わりにダウンミリングを使用することです。 6番目のステップは、純粋な鉱油を使用して、耐熱チタン合金と析出硬化ステンレス鋼の切断領域を低速で洗浄することです。
4.ブレードが壊れたりナイフに当たったりする
この種のエッジチッピングには多くの理由があります。 刃の材質が硬すぎたり、刃の形状が弱すぎたり、切削速度が遅すぎたりすると、刃先がつぶれて、被削材が不均一になったり、断続的に切削されたりすることがあります。
このような状況を考慮して、まず、シムが破損していないか、ブレードのネジが変形していて交換が必要かどうかを確認します。 第二に、振動係数を排除し、より靭性の高いブレード材料を使用し、エッジの強いブレードを交換する必要があります。 最後に、刃先をなくすために切削速度を上げる必要があります。口がつぶれる可能性があります。 (関連記事:機械加工摩耗の問題と解決策の要約)