金属切削液は切削液と略されます。 切削工程での潤滑効果により、すくい面と切りくず、逃げ面と加工面の間の摩擦を低減し、潤滑膜の一部を形成することで、切削抵抗、摩擦、消費電力を低減します。 工具とワークブランク間の摩擦部の表面温度と工具摩耗を低減し、被削材の切削性能を向上させます。
切削プロセスが異なれば、切削液の要件も異なります。 適切な切削液を正しく選択することは、ワークピースの品質にとって非常に重要です。
荒削り
荒削りの場合、加工許容値が大きいため、切削深さや送りが大きく、切削抵抗が大きく、切削熱が多く発生し、工具摩耗も深刻です。 主に冷却に使用し、特定の洗浄、潤滑、防錆を行います。 効果的な水性切削液は、時間内に切削熱を取り除き、切削温度を下げ、工具の耐久性を向上させます。 一般的に、極圧エマルジョンを使用することをお勧めします。 優れた冷却性能に加えて、極圧エマルジョンは優れた極圧潤滑性も備えています。 水性切削液を使用する場合は、工作機械のガイドレール面のメンテナンスに注意してください。 作業台で切削液を乾燥させ、潤滑剤を塗布してから作業を終了してください。
仕上げ旋削
旋削終了時の切削代は小さく、切削深さは一般的に0.05〜0.8mmと少なく、送り速度も小さいです。 ワークの精度と表面粗さを確保する必要があります。 切削抵抗が低く、仕上げ旋削時の温度が低いため、摩擦係数が低く、潤滑性能の良い切削液を使用する必要があります。 一般に、高濃度(質量分率が10%を超える)のエマルジョンと油性添加剤を含む切削液を使用する必要があります。 細糸、菜種油、大豆油などの高精度要件で旋削する場合は、精度要件を満たすために潤滑液として使用する必要があります。 前述のように、植物油の安定性が悪く、酸化しやすいため、精密切削油としてJQ-1精密切削油15%、L-AN32全損システム油85%を使用している工場もあり、良好な結果が得られています。
つまらない仕事
ボーリングのメカニズムは旋削と同じですが、内穴加工であり、切削量や切削速度は大きくありませんが、放熱条件が悪く、エマルジョンが切削液として使用でき、流れがあります。 必要に応じて、切削液の圧力を適切に上げる必要があります。
ミリング
フライス盤は断続的な切削です。 各歯の切削深さは時々変化し、振動や一定の衝撃を受けやすいため、フライス盤の状態は旋削よりも悪くなります。 高速フラットミリングまたは高速エンドミル加工に高速度鋼工具を使用する場合、極圧エマルジョンなど、優れた冷却特性と特定の潤滑特性を備えた切削液が必要です。 低速フライス盤では、精密切削油や不活性極圧切削油など、潤滑性の良い切削油が必要です。 ステンレス鋼および耐熱合金鋼には、硫黄および塩素極圧添加剤を含む切削油を使用できます。
リーマ
リーマは穴の仕上げであり、高精度が必要です。 リーマ加工は、主に工具と穴の壁を絞って切削するため、低速で小送りの切削です。 また、切りくずの破片が溝に留まったり、ブレードの端に付着したりしやすく、土地の圧搾効果に影響を与えます。 加工精度と表面粗さを破壊し、切削トルクを増加させるだけでなく、構成刃先を生成し、工具の摩耗を増加させます。 リーマは基本的に境界潤滑の状態に属します。 一般に、高濃度の極圧エマルジョンまたは良好な潤滑性と一定の流動性を備えた極圧切削油を使用して、良好な結果を得ることができます。 ステンレス鋼、耐熱鋼の場合、極圧の高い複合切削液を使用できます。 深穴リーマの場合、潤滑性能の良い深穴穴あけ切削油が技術的要件を満たすことができます。
ブローチ
ブローチは、刃の歯に合わせて軸方向に多数の歯を配置した加工工具です。 ブローチ加工の特徴は、複雑な形状のワークを高精度に加工できることです。 ブローチは貴重な工具であるため、工具の耐久性は製造コストに大きな影響を与えます。 また、ブローチ加工は仕上げ加工であり、ワークの表面粗さには厳しい要件があります。 ブローチ加工は、切削抵抗が大きく、切りくず除去が困難で、冷却状態が悪く、ワーク表面に傷がつきやすいため、切削液の潤滑性と切りくず除去性能が求められます。 中国には硫黄極圧添加剤を含む特殊なブローチオイルがあります。
ステンレス鋼および耐熱合金のブローチ加工には、次の式(質量分率)を使用できます:JQ-2極圧潤滑剤20%、塩素化パラフィン15%、ベンゼン80使用1%、L-ANN22全損失システムオイル64%。
掘削
一般的なツイストドリルによる穴あけは荒加工です。 穴あけ時に切りくずを取り除くのが難しく、切削熱が出にくく、刃の焼きなましが発生し、ドリルの耐用年数や加工効率に影響を与えることがよくあります。 性能の良い切削液を選択することで、ドリルの寿命を数倍以上延ばすことができ、生産効率も大幅に向上します。 一般的に、極圧エマルジョンまたは極圧合成切削液を使用することができます。 極圧合成切削液は、表面張力が低く、透過性に優れています。 ドリルを適時に冷却できるため、工具寿命を延ばし、加工効率を向上させるのに非常に効果的です。 ステンレス鋼や耐熱合金などの切削が難しい材料には、低粘度の極圧切削油を使用できます。
ねじ加工
ねじ切りの場合、工具は切削材料とくさび形で接触し、刃先は三方を切削材料で囲まれます。 切削トルクが大きく、切りくず除去が困難です。 時間内にチップが熱を奪うことはできません。 工具は摩耗しやすく、切削破片が詰まり、振動が発生しやすくなっています。 特にねじ切りやタッピングの場合、切削条件が厳しく、チッピングやタップ切れが発生する場合があります。
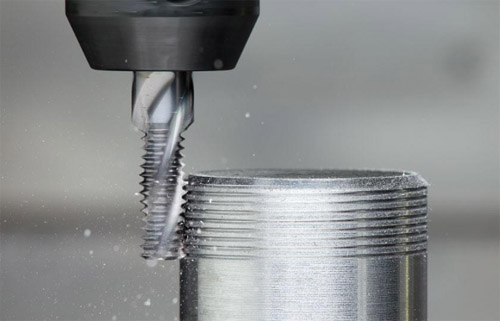
切削液は、工具の摩擦抵抗を低減し、工具の寿命を延ばすために、摩擦係数を低くし、極圧を高くする必要があります。 一般的に、油性薬剤と極圧剤の両方を含む複合切削液を選択する必要があります。 さらに、糸を叩くとき、切削液の透過性は非常に重要です。 切削液が時間内に刃先に浸透できるかどうかは、タップの耐久性に大きな影響を与えます。 切削液の透磁率は粘度に関係します。 低粘度のオイルは透過性が高くなります。 必要に応じて、透過性を向上させるために少量のディーゼルまたは灯油を追加することができます。 止まり穴をタップすると、切削液が入りにくい場合があります。 止まり穴をタップすると、切削液が入りにくい場合があります。
タッピング用の切削液のいくつかの式(質量分率)は次のとおりです。
- 硫酸化脂肪油10%、塩素化パラフィン10%、脂肪油8%、L-AN15全損油72%、鋼および合金鋼のタッピングスレッドに適しています。
- JQ-2極圧潤滑剤20%、JQ-1精密切削潤滑剤10%、L-AN15全損失システムオイル70%、鋼および合金鋼のタッピングに適しています。
- JQ-2極圧潤滑剤15%、ディーゼルエンジンオイル20%、L-AN15全損失システムオイル65%、アルミニウムおよびアルミニウム合金のタッピングに適しています。
- JQ-2極圧潤滑剤30%、塩素化パラフィン10%、脂肪油10%、L-AN32全損失システム油50%、ステンレス鋼および止まり穴タッピングに適しています。
- 極圧乳化油20%+水80%、鋼標準部品のねじ加工に適しています。
研削
研削加工により、高い寸法精度と低い表面粗さを得ることができます。 粉砕時は粉砕速度が速く、発熱が大きく、粉砕温度は800〜1000℃以上になります。 熱応力により、ワークの表面焼けや表面亀裂、部品変形が発生しやすくなります。 砥石が不動態化して研削粒子が脱落し、砥石や砥石粉が部品の表面に飛び散り、落下しやすくなり、加工精度や表面粗さに影響を与えます。 強靭なプラスチック材料を加工する場合、砥石の作業面の隙間や砥石に削りくずが入りやすい 砥石の表面に加工金属が溶け込んでいるため、砥石の研削能力が低下します。 したがって、研削温度を下げ、砥石や砥石粉を洗い流し、研削比やワークの表面品質を向上させるためには、冷却性能や洗浄性能に優れた切削液を使用する必要があります。 ある程度の潤滑性と防錆性があります。
1.通常の粉砕:
防錆エマルジョンまたはソーダ水および合成切削液(質量分率)を使用できます。たとえば、防錆エマルジョン2%、亜硝酸ナトリウム0.5%、炭酸ナトリウム0.2%、水97.3%。 0.8%亜硝酸ナトリウム、0.3%炭酸ナトリウム、0.5%グリセリン、98.6%水; 3%〜4%の防錆エマルジョンまたは化学合成液を直接使用してください。
高精度が要求される精密研削の場合、H-1微粉砕液を使用することで、ワークの加工精度と研削効率を大幅に向上させることができ、使用濃度は4〜5%です。
2.高速研削:
ホイール速度が50m / sを超える研削は、通常、高速研削と呼ばれます。 砥石の線速度が上がると、砥石温度が大幅に上昇します。 試験によると、砥石の線速度が60m / sのときの研削温度(ワークの平均温度)は、30m / sよりも約50〜70%高くなっています。 砥石線速度が80m / sの場合、60m / sよりも砥石温度が高くなります。 15〜20%高い。 砥石の線速度を上げると、単位時間に研削に関与する砥粒の数が増え、摩擦が激しくなり、エネルギー消費量も増えて、ワークの表面温度が上がります。 表面に火傷やひびが入る可能性が高くなります。 効率的な冷却性能を備えたクーラントを使用して解決します。 そのため、高速研削では通常の研削液は使用できませんが、浸透性、冷却性能に優れた高速研削液を使用する必要があります。 たとえば、GMY高速粉砕液は、60m / sクレームの線速度で高速粉砕プロセスに対応できます。
3.パワーグラインディング:
これは、高度な高効率粉砕プロセスです。 例えば、プランジカット高速で強力な研削では、直線速度60m / sの砥石を3.5〜6mm / minの送り速度で半径方向に切削します。 レートは20〜40mm3 /mm.sまで高くなる可能性があります。 このとき、砥石の砥粒とワークの摩擦が非常に大きくなります。 高圧大流量の冷却条件下でも、摩擦ゾーンのワークピースの表層の温度範囲は700〜1000℃です。 いいえ、粉砕プロセスは不可能です。 プランジフォース粉砕では、エマルジョンと比較して、総粉砕量が35%増加し、粉砕率が30〜50%増加し、通常の粉砕時間が約40%延長されます。 電力損失は約40%です。 したがって、クーラントの性能は、強研削時の研削効果に大きく影響します。 現在、国産の強研削液には、QM高速強研削液とHMスローフィード強研削液があります。
4.ダイヤモンド砥石研削:
硬合金、セラミック、ガラスなどの硬度の高い材料の研削に使用されます。 粗く、細かく粉砕することができます。 地面は一般に亀裂や隙間を生じないため、より良い低表面粗さを実現できます。 研削時の過度の発熱や砥石の早期摩耗を防ぎ、表面粗さを小さくするためには、継続的かつ十分な冷却が必要です。 ワークの硬度が高いため、砥石を鋭利に保つために、研削液は主に冷却性能と洗浄性能を備えている必要があります。 研削液の摩擦係数が低すぎないようにしてください。低すぎると、研削効率が低下し、表面が焼けてしまいます。 粉砕液には無機塩をベースにした化学合成液を使用しています。 微粉砕時に潤滑剤として少量のポリエチレングリコールを添加することができ、ワークピースの表面処理品質を向上させることができます。 加工精度の高い部品には、潤滑性に優れた低粘度の油性研削液を使用できます。
5.ねじ山、歯車、ねじ研削:
このタイプの研削は、研削後の加工面の品質と寸法精度に特別な注意を払っています。 一般的に、極圧添加剤を含む砥石を使用することをお勧めします。 このタイプの油性研削液は、その優れた潤滑性能により、研削熱を低減でき、その中の極圧添加剤がワークピースの材料と反応して、低せん断強度の硫化鉄膜と塩化鉄膜を生成します。 砥粒の刃先の摩耗を減らし、研削をスムーズに行うことができます。 より良い冷却および洗浄特性を得るために、そして火災安全を確保するために、低粘度および高引火点の研削油を選択する必要があります。